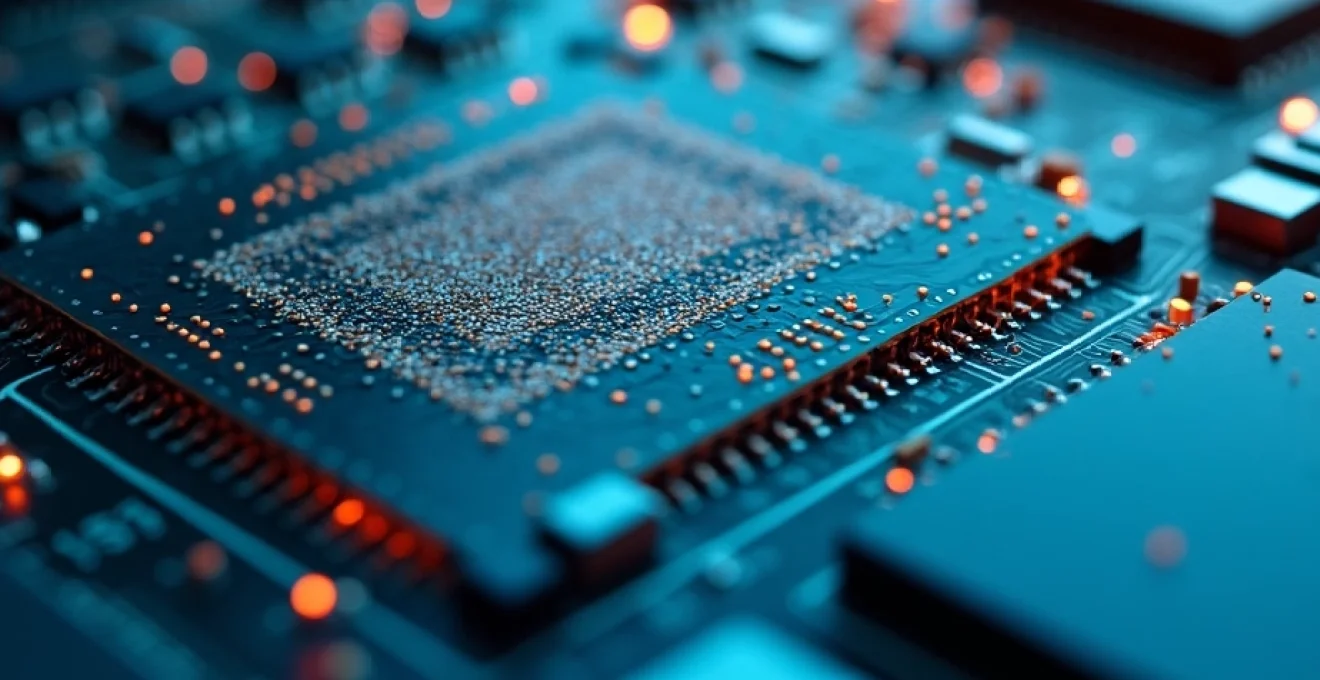
L’evoluzione tecnologica nel settore dell’elettronica ha portato a significativi cambiamenti nella progettazione e produzione di circuiti stampati. I Rigid-Flex PCB rappresentano una delle innovazioni più interessanti degli ultimi anni, combinando le caratteristiche dei circuiti rigidi tradizionali con la flessibilità dei circuiti flessibili. Questa tecnologia ibrida sta rivoluzionando numerosi ambiti applicativi, offrendo soluzioni avanzate per dispositivi sempre più compatti e performanti.
L’impatto dei Rigid-Flex PCB si estende dall’industria aerospaziale alla medicina, passando per le telecomunicazioni e l’elettronica di consumo. La loro capacità di adattarsi a spazi ridotti e conformazioni tridimensionali complesse li rende particolarmente adatti per applicazioni dove peso, ingombro e affidabilità sono fattori critici. Ma quali sono effettivamente le differenze sostanziali rispetto ai circuiti tradizionali? E in quali ambiti offrono vantaggi concreti?
Struttura e composizione dei Rigid-Flex PCB
I Rigid-Flex PCB si distinguono per la loro struttura ibrida che combina aree rigide e flessibili all’interno dello stesso circuito stampato. La parte rigida è tipicamente realizzata in materiali come FR-4 o ceramica, mentre le sezioni flessibili utilizzano substrati come poliimmide o poliestere. Questa configurazione permette di ottenere circuiti con caratteristiche uniche, in grado di piegarsi e conformarsi a geometrie complesse mantenendo al contempo zone di stabilità per il montaggio dei componenti.
La struttura di un Rigid-Flex PCB è generalmente composta da più strati, con le aree flessibili che fungono da interconnessione tra le diverse zone rigide. I layer conduttivi in rame sono depositati sia sulle parti rigide che su quelle flessibili, garantendo continuità elettrica attraverso l’intero circuito. La transizione tra le zone rigide e flessibili rappresenta un punto critico del design, richiedendo particolare attenzione per evitare stress meccanici e garantire l’integrità delle connessioni.
Un aspetto fondamentale dei Rigid-Flex PCB è la capacità di integrare componenti elettronici sia nelle aree rigide che in quelle flessibili. Questo permette di ottimizzare il layout del circuito, posizionando i componenti nelle zone più funzionali e riducendo la necessità di connessioni esterne. La flessibilità intrinseca di questi circuiti consente inoltre di realizzare design tridimensionali complessi, impossibili da ottenere con PCB tradizionali.
La vera innovazione dei Rigid-Flex PCB risiede nella loro capacità di adattarsi dinamicamente alle esigenze di spazio e forma, mantenendo al contempo elevate prestazioni elettriche e meccaniche.
Caratteristiche tecniche dei circuiti tradizionali
I circuiti stampati tradizionali, comunemente noti come PCB rigidi, rappresentano ancora oggi la soluzione più diffusa per la realizzazione di schede elettroniche. La loro struttura è caratterizzata da un substrato rigido, tipicamente in FR-4 (un materiale composito di fibra di vetro e resina epossidica), sul quale vengono depositati uno o più strati di rame per realizzare le piste conduttive.
I PCB rigidi offrono diversi vantaggi in termini di stabilità meccanica, resistenza termica e facilità di produzione su larga scala. La loro rigidità intrinseca fornisce un supporto stabile per il montaggio dei componenti elettronici, garantendo connessioni affidabili e resistenti alle sollecitazioni. Inoltre, la planarità delle superfici facilita i processi di assemblaggio automatizzato, riducendo i costi di produzione per grandi volumi.
Una caratteristica distintiva dei circuiti tradizionali è la possibilità di realizzare strutture multistrato complesse, con un elevato numero di layer interconnessi tramite fori metallizzati ( vias ). Questa configurazione permette di ottenere design ad alta densità, supportando circuiti digitali veloci e applicazioni RF avanzate. Tuttavia, la rigidità intrinseca dei PCB tradizionali pone limiti significativi in termini di flessibilità di design e adattabilità a geometrie non planari.
Vantaggi prestazionali dei Rigid-Flex PCB
I Rigid-Flex PCB offrono una serie di vantaggi prestazionali che li rendono particolarmente attraenti per applicazioni avanzate in diversi settori industriali. La loro natura ibrida consente di superare molte delle limitazioni tipiche dei circuiti tradizionali, aprendo nuove possibilità di design e ottimizzazione.
Resistenza alle vibrazioni e flessioni
Uno dei principali vantaggi dei Rigid-Flex PCB è la loro eccezionale resistenza alle vibrazioni e alle sollecitazioni meccaniche. La presenza di aree flessibili permette di assorbire e distribuire gli stress meccanici in modo più efficace rispetto ai PCB rigidi tradizionali. Questa caratteristica li rende ideali per applicazioni in ambienti soggetti a forti vibrazioni, come nel settore automotive o aerospaziale.
La capacità di sopportare flessioni ripetute senza compromettere l’integrità delle connessioni elettriche è un altro punto di forza dei Rigid-Flex PCB. Alcuni design possono resistere a migliaia di cicli di piegatura, garantendo una durata operativa prolungata in dispositivi che richiedono movimenti frequenti, come nei display pieghevoli o nelle apparecchiature medicali portatili.
Riduzione del peso e dello spazio occupato
La possibilità di eliminare connettori e cavi esterni rappresenta un vantaggio significativo dei Rigid-Flex PCB in termini di riduzione del peso e dell’ingombro complessivo. Integrando le interconnessioni direttamente nel circuito flessibile, è possibile ottenere design più compatti e leggeri, aspetto cruciale in settori come l’elettronica indossabile o i dispositivi mobili.
L’ottimizzazione dello spazio si traduce anche in una maggiore libertà di progettazione, consentendo di realizzare forme tridimensionali complesse che si adattano perfettamente agli spazi disponibili. Questo aspetto è particolarmente rilevante nelle applicazioni dove ogni millimetro conta, come nei satelliti o nei dispositivi medici impiantabili.
Miglioramento dell’affidabilità delle interconnessioni
La riduzione del numero di connessioni esterne e saldature porta a un miglioramento significativo dell’affidabilità complessiva del sistema. I Rigid-Flex PCB consentono di eliminare punti di failure potenziali associati a connettori e cavi, riducendo il rischio di malfunzionamenti dovuti a disconnessioni o rotture dei contatti.
Inoltre, la continuità elettrica garantita dalle aree flessibili permette di ottenere prestazioni superiori in termini di integrità del segnale, specialmente per applicazioni ad alta frequenza. La possibilità di controllare con precisione l’impedenza lungo tutto il percorso del segnale, incluse le zone di transizione tra aree rigide e flessibili, rappresenta un vantaggio competitivo importante per i Rigid-Flex PCB.
L’eliminazione di connessioni esterne e la riduzione dei punti di failure potenziali rendono i Rigid-Flex PCB una scelta eccellente per applicazioni che richiedono massima affidabilità in condizioni operative critiche.
Applicazioni specifiche dei Rigid-Flex PCB
I vantaggi unici offerti dai Rigid-Flex PCB li rendono particolarmente adatti per una vasta gamma di applicazioni avanzate in diversi settori industriali. La loro versatilità e le prestazioni superiori in termini di flessibilità, compattezza e affidabilità aprono nuove possibilità di design e ottimizzazione in ambiti dove i circuiti tradizionali mostrano limiti evidenti.
Utilizzo nell’industria aerospaziale
Nel settore aerospaziale, dove peso, spazio e affidabilità sono fattori critici, i Rigid-Flex PCB rappresentano una soluzione ideale. La loro capacità di conformarsi a geometrie complesse li rende perfetti per l’integrazione in strutture aerodinamiche, consentendo di ottimizzare lo spazio disponibile all’interno di velivoli e satelliti. La resistenza alle vibrazioni e agli shock termici tipici dell’ambiente spaziale è un altro aspetto che favorisce l’adozione di questa tecnologia.
Un esempio concreto di applicazione è nei sistemi di controllo di volo, dove i Rigid-Flex PCB permettono di realizzare interconnessioni complesse tra diverse unità, riducendo il peso complessivo e migliorando l’affidabilità rispetto alle soluzioni basate su cablaggio tradizionale. La flessibilità intrinseca di questi circuiti facilita inoltre le operazioni di manutenzione e aggiornamento dei sistemi avionici.
Implementazione nei dispositivi medici impiantabili
Nel campo dei dispositivi medici impiantabili, i Rigid-Flex PCB offrono vantaggi significativi in termini di miniaturizzazione e biocompatibilità. La possibilità di realizzare circuiti compatti e conformabili permette di sviluppare dispositivi come pacemaker, defibrillatori impiantabili e neurostimolatori di dimensioni sempre più ridotte, migliorando il comfort del paziente e riducendo i rischi associati all’intervento chirurgico.
La resistenza alla flessione ripetuta e l’elevata affidabilità delle interconnessioni sono caratteristiche cruciali per garantire la longevità e la sicurezza dei dispositivi impiantati. Inoltre, l’utilizzo di materiali biocompatibili nelle aree flessibili riduce il rischio di reazioni avverse del corpo umano, aspetto fondamentale per applicazioni a lungo termine.
Adozione nei sistemi di telecomunicazione 5G
L’evoluzione verso le reti 5G richiede soluzioni circuitali in grado di gestire frequenze sempre più elevate mantenendo dimensioni compatte. I Rigid-Flex PCB si stanno affermando come tecnologia chiave per lo sviluppo di antenne e moduli RF ad alte prestazioni. La possibilità di integrare elementi radianti flessibili con circuiti di controllo rigidi in un unico assembly offre vantaggi significativi in termini di prestazioni e miniaturizzazione.
Nei sistemi di telecomunicazione base station, i Rigid-Flex PCB consentono di ottimizzare il layout delle antenne MIMO (Multiple Input Multiple Output), fondamentali per le tecnologie 5G. La flessibilità di design permette di adattare le antenne a diverse configurazioni e spazi di installazione, migliorando l’efficienza spettrale e la copertura del segnale.
Processi di fabbricazione a confronto
La produzione di Rigid-Flex PCB richiede processi di fabbricazione più complessi rispetto ai circuiti tradizionali, con conseguenti implicazioni in termini di costi e tempi di realizzazione. Il processo inizia con la laminazione dei materiali flessibili e rigidi, seguita da una serie di passaggi che includono la creazione dei fori, la metallizzazione, l’incisione dei circuiti e l’applicazione di maschere protettive.
Un aspetto critico nella fabbricazione dei Rigid-Flex PCB è la gestione delle zone di transizione tra aree rigide e flessibili. Queste aree richiedono particolare attenzione per evitare stress meccanici che potrebbero compromettere l’integrità del circuito. Tecniche avanzate come l’utilizzo di adesivi speciali e processi di laminazione controllata vengono impiegate per garantire la robustezza di queste zone critiche.
Al contrario, la produzione di PCB rigidi tradizionali segue processi consolidati e altamente automatizzati, che consentono una maggiore efficienza produttiva, specialmente per grandi volumi. La standardizzazione dei materiali e dei processi permette di ottenere economie di scala difficilmente raggiungibili con i Rigid-Flex PCB, almeno nelle attuali condizioni di mercato.
Considerazioni di costo e scalabilità produttiva
L’adozione dei Rigid-Flex PCB comporta considerazioni importanti in termini di costi e scalabilità produttiva. Il costo unitario di un Rigid-Flex PCB è generalmente superiore rispetto a un circuito tradizionale equivalente, principalmente a causa della maggiore complessità dei processi di fabbricazione e dei materiali utilizzati. Tuttavia, è fondamentale considerare il costo totale di sistema quando si valuta l’opportunità di adottare questa tecnologia.
I vantaggi in termini di riduzione del peso, dell’ingombro e del numero di componenti possono tradursi in risparmi significativi a livello di sistema complessivo. Ad esempio, nell’industria aerospaziale, la riduzione del peso ottenibile con i Rigid-Flex PCB può portare a notevoli risparmi in termini di consumo di carburante nel corso della vita operativa di un velivolo.
La scalabilità produttiva rappresenta una sfida importante per l’industria dei Rigid-Flex PCB. Mentre la produzione di PCB rigidi tradizionali beneficia di processi altamente automatizzati e standardizzati, la fabbricazione di Rigid-Flex richiede ancora un elevato grado di personalizzazione e intervento manuale. Questo aspetto limita attualmente le possibilità di produzione su larga scala, impattando sui costi unitari.
Tuttavia, l’innovazione tecnologica sta portando a progressivi miglioramenti nei processi produttivi dei Rigid-Flex PCB, con l’obiettivo di aumentarne la scalabilità e ridurne i costi. L’adozione di tecniche di progettazione assistita da computer (CAD) specifiche per i Rigid-Flex e l’ottimizzazione dei flussi di lavoro stanno contribuendo a semplificare e standardizzare i processi di fabbricazione.
Un aspetto chiave per migliorare la scalabilità produttiva è lo sviluppo di materiali flessibili più performanti e compatibili con i processi di produzione dei PCB rigidi. Questo permetterebbe di sfruttare meglio le linee produttive esistenti, riducendo la necessità di macchinari e processi dedicati esclusivamente ai Rigid-Flex.
Nonostante le sfide attuali, le previsioni di mercato indicano una crescita significativa della domanda di Rigid-Flex PCB nei prossimi anni, trainata dall’evoluzione di settori come l’IoT, i dispositivi indossabili e l’elettronica medicale. Questo aumento dei volumi produttivi dovrebbe portare a economie di scala e a una progressiva riduzione dei costi unitari, rendendo la tecnologia Rigid-Flex sempre più competitiva rispetto alle soluzioni tradizionali.
L’evoluzione tecnologica e l’aumento della domanda stanno gradualmente colmando il divario di costo tra Rigid-Flex PCB e circuiti tradizionali, aprendo nuove opportunità di applicazione in settori finora dominati dai PCB rigidi.
Mentre i Rigid-Flex PCB presentano attualmente costi di produzione più elevati e sfide in termini di scalabilità rispetto ai circuiti tradizionali, i loro vantaggi unici in termini di design, prestazioni e affidabilità li rendono una scelta sempre più attraente per applicazioni avanzate. La continua innovazione nei processi produttivi e nei materiali, unita alla crescente domanda di mercato, sta progressivamente migliorando il rapporto costo-beneficio di questa tecnologia, prospettando un futuro in cui i Rigid-Flex PCB potrebbero diventare una soluzione mainstream in molti settori dell’elettronica.